Moore Forest Makes The Grade In Hardwoods
By Wayne Miller
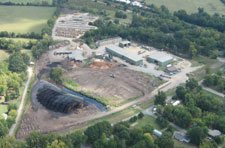 |
This is an aerial view of Moore Forest Products Inc.’s headquarters in Kensett, Ark. |
Kensett, Ark.—For more than 30 years, Moore Forest Products Inc., headquartered here, has provided precision manufactured Hardwood lumber, switch ties and other forest products to customers located throughout the United States.
Jerry Moore has a long history in the forest products industry that includes pulpwooding and logging with his father in east Texas. Jerry also worked for International Paper Co. (IP) for many years before getting his own pulpwood dealership at Judsonia, Ark., with IP in 1966. This led to a relationship with a man named Fred Beaman whom Jerry sold Hardwood logs to that he procured with pulpwood he bought. Moore Forest Products Inc. was established in November 1976 when Jerry Moore bought Fred Beaman Lumber Co. from Fred Beaman (it was a small tie mill).
Jerry’s son, Steve Moore, who today serves as president, joined the company upon graduating from the University of Arkansas in Monticello.
Steve said, “When I graduated from the University of Arkansas in May 1977, I came to work here the next day.”
 |
Key employees at Moore Forest Products include Terry Dees, vice president and general manager; Steve Moore, president; and Mitch Moore, Steve’s son, sales and office controller. |
Steve, who has a bachelor’s degree in forestry, is actually a third generation working in the forest products industry as his grandfather owned a pulpwood business in east Texas.
Moore Forest Products Inc., which is located on 28 acres just east of Searcy, Ark., manufactures 8 million board feet of 4/4 grade lumber, 4x6 cants and switch ties in Red and White Oak, Sap Gum, Poplar, Hackberry, Elm, Ash, Soft Maple and cypress.
Steve said the company procures its logs from within a 130-mile radius of Kensett. A majority of the timber is purchased as tracts that Moore Forest Products pays contractors to log. The remainder is bought as “gatelogs” according to their grade from other loggers.
“In 1977, when I came to work here, a long haul to obtain logs was 30 miles,” he said. “Today, we have to go out 130 miles because of the dwindling supply of timber.”
In addition to availability, Steve said the biggest challenge in the marketplace today is buying logs at a reasonable price. “Log prices have not followed the lumber market, at least not in the South,” he said. “There’s always some company that’s holding prices up. If you try to lower prices, you won’t get any logs at all. We’re paying too much for our logs and not getting enough for our lumber.”
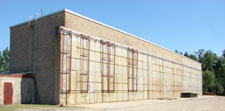 |
Moore Forest Products operates three Spears dry kilns, which have a total capacity of 210,000 board feet.
|
When logs first arrive in Kensett, they are unloaded by one of two 950 Caterpillar front-end loaders to the log scaler, which scales and grades the logs. Moore Forest Products utilizes a HMC debarker, Corley carriage with a scanner and a six-foot McDonough headrig with “six-foot wheels and a 7-foot opening.”
“Six-foot wheels and a 7-foot opening means the wheels are further apart, and it requires a longer saw to complete the job,” Steve said. “The longer your saw is, the longer it’s going to last.”
The Corley carriage cuts the logs into lumber and large cants. The cants are then sent to the computerized Corley linebar resaw. There is a six-foot Kockums band at the linebar, which cuts grade lumber, ties and cants.
Steve said he has a lot of Corley equipment in his operation because it’s a “superior product and offers great service.”
Moore Forest Products operates three Spears dry kilns, which has a total capacity of 210,000 board feet. However, only one is currently operating, “because there is not a large enough price spread between green and kiln-dried lumber to pay the extra cost of kiln drying,” Steve said. “Running one kiln costs about the same as three kilns cost three years ago. This is when we look back and say we wish we had put in a waste-fired boiler years ago.”
 |
The company uses a unique chip pile loading system to store its wood waste. |
Steve said the success of Moore Forest Products Inc. has been based on the hard work of its employees and the loyalty of its repeat customers.
“We sell strictly on grade, and we’re very careful to make that grade right,” he said. “We do a good job of edging our lumber and all lumber is double end trimmed at the sawmill. We offer kiln drying, S2S and rail, truck and container shipments. We put up great looking packs of lumber for our customers.”
Steve added that the company is well positioned for future growth and success. “We’ve got a good location here in Kensett,” he said. “We’re farther west than most of the other Hardwood sawmills in Arkansas, so we’ve been able to sell a lot of lumber into Texas. We’re located just two miles from a major freeway (U.S. 67/167), and we’re on the Union Pacific railroad line.”
Moore Forest Products Inc. sells its lumber green and kiln-dried to brokers and end users throughout the United States. Over the years, the firm has also sold its products to distribution yards, including a customer in Mexico who requested No. 1 Common Red Oak. Red and White Oak are the predominant species sold as Hardwood lumber, and White Oak makes up approximately 28 percent of Oak lumber sales.
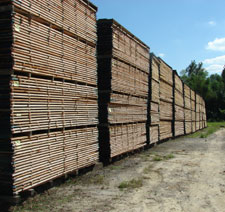 |
This is a picture of some Oak lumber air drying in the yard. |
Koppers Inc., an integrated producer of carbon compounds and treated wood products, located in Pittsburgh, Pa., is one of the largest customers of Moore Forest Products’ switch ties. However, the company markets its switch ties on the open market. “We will sell our switch ties to anybody who wants to buy them,” Steve said. “We just have a very good working relationship with Koppers. Their representative that covers this area actually lives in Searcy, Ark., where we live, and we know him personally.”
Steve said his firm ships most of its products by truck, but averages one railcar load per month. The facility has a good customer up north that receives railcar shipments.
Moore Forest Products Inc. has approximately 42 workers on staff. In addition to Jerry Moore, who is semi-retired but still comes in every day, and Steve Moore, who handles Hardwood lumber sales and purchasing, key employees include Mitch Moore, Steve’s son, sales and office controller; Terry Dees, vice president and general manager; and Tom Berry III, timber and log procurement. Steve said, “Our employees are key to our success. Some were here when I came to work here.”
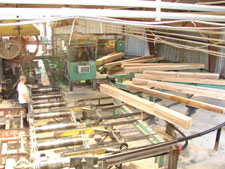 |
Moore Forest Products utilizes this Corley linebar resaw as well as other Corley equipment. |
The company is a member of the National Hardwood Lumber Assoc. (NHLA) and the Southeastern Lumber Manufacturers Assoc. Inc. Jerry Moore is a former member of the NHLA board of directors.
For more information, contact Moore Forest Products Inc. at 501-742-3371, fax 501-742-3423 or e-mail sdmoore@centurytel.net.
 |
Jeff Williams has been a lumber grader at Moore Forest Products for many years. |
|